The global computer chip shortage has at this point affected nearly every global industry and many in the IT sector will have had some experience with it directly, writes Jim Walters, a Support Analyst at Foundation IT. The shift to homeworking caused by the pandemic was one of the main causes, as organisations worldwide scrambled to equip their staff with the necessary equipment to continue their work at home while offices had to close.
Shortages are, as a result, dramatically pushing up the price of chips and graphics cards compared to pre-pandemic prices, with business struggling to deliver to customer requirements, fulfil orders and IT teams unable to provide the infrastructure and technology required for organisations to innovate.
Obtaining computer hardware has been difficult for individuals and businesses alike, whether due to a restricted supply of Graphics Processing Unit (GPU) hardware impacting the release of the latest generation of games consoles and gaming GPUs, the supply of critical components for the manufacturing of cars causing production lines to halt, or, as recently reported, payment card manufacturers signalling that they are having difficulties securing the components required for credit cards. Procurement of computer hardware has become more difficult, with inflated costs and longer lead time and it seems that the supply issues are here to stay; many industry commentators are predicting that this situation will be with us for another two years.
See also: Tackling large-scale transformation of legacy systems with automation: 25m lines of mainframe code, 10.7b rows of data…
The question for IT is, how can we mitigate the issues that working from home directives, compounded with global chip supply problems have caused to businesses that we support and work with? As an example, Bedford Pumps, a British manufacturer of robust pumping plants for the water and wastewater industry that we work with was struggling to procure powerful, 3D capable laptops or desktops for its design teams during the pandemic. The lead time on delivery was long and unpredictable and at the worst points simply unknown, and costs were inflated. It also had issues with teams using existing machines from home during the pandemic - even if they could source them. To address the challenge, Bedford Pumps, a business that relies on hardwired, computer chip systems for its CAD/CAM product design systems, had to get creative and think outside of the box for its IT infrastructure.
The company needed a quick resolution to prevent any downtime and ensure it could continue to design and deliver products. By implementing Azure Virtual Desktop (previously Windows Virtual Desktop) powered by an AMD machine SKU, this provided 3D capable virtual desktops that have the necessary processing power to cope with the complex designs in Solidworks, the computer-aided design and engineering program used by Bedford Pumps. Azure Virtual Desktop, in the right environment, can be off the ground in an afternoon, so much faster than installing powerful 3D machines. Users still need a computer to connect to the remote desktop, but it provides a far faster and more flexible solution which the business can repurpose on other machines, whether that be an older device or even a personal device.
The challenges and benefits
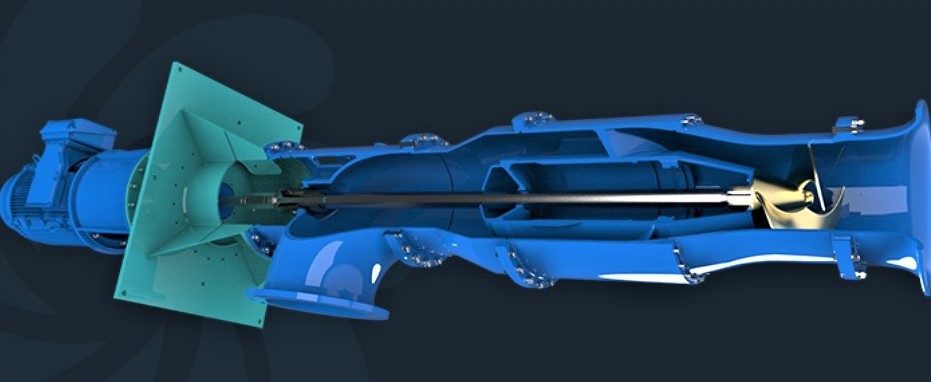
The deployment has not been without its challenges. There were times where the virtual machines haven’t been able to start due to capacity issues, as global demand for the machines has at times simply outpaced the ability for Microsoft to supply them. We worked around this by temporarily utilising other machine sizes, which could be a more or less powerful machine than planned, as a short-term solution.
Moving users onto Azure Virtual Desktop, whether that be the more typical office user, or those with specific demands for CAD/CAM 3D design processes such as Bedford Pump, enables businesses to extend the use of their existing hardware well beyond its typical lifespan. Supporting IT infrastructure resources can also be migrated alongside the desktop, such as file servers and databases, which can improve the user experience, as the latency between the desktop and these services is reduced and keeps the company data in a more controlled environment when staff are working remotely.
Overall, with cloud enabled CAD/CAM the team at Bedford Pumps, who are usually reliant on powerful 3D machines for their CAD/CAM programmes, were able to continue working remotely during lockdown and often with improved performance and greater connectivity. The business has much greater control of its machines and everything can now be scaled out and in, as required, only paying for the underlying virtual machines when needed. New machines can be provisioned quickly for new users or upgraded for increased requirements without the complexities of shipping devices. Similarly, if a user no longer requires the desktop, the resources can be recovered and reallocated easily.
Even as pandemic restrictions are slowly lifted and computer chips and equipment become more available, it's widely acknowledged that many organisations and workers will continue working from home. The move towards cheaper hardware, and the ability to connect to a cloud hosted desktop provides a clear business benefit that is likely here to stay.